Using Computational Fluid Dynamics (CFD), we can simulate and analyze complex problems involving fluid-fluid, fluid-solid, or fluid-gas interaction. Our experts work across a broad range of industries and throughout the component lifecycle to help you get the best value from your assets.
How does CFD simulation work?
Element uses advanced computational methods to study complex fluid dynamics and heat transfer problems that affect our customer’s components and products in the environment and operating conditions.
For example, we can look at the turbulent flow on an aircraft wing section and how it behaves at different angles of incidence. The domain in this instance would be the airflow around the wing, which we would upload into our CAD software, measure and combine with boundary conditions, and pass to our experts to produce a solution. Element can extract critical areas of interest, for example, the lift, the different angles of attack, or the drag theories.
CFD applications
Our experts can apply fluid dynamic principles to a wide range of complex, industrially relevant applications, including:
- Fluid-structure interaction can help you understand the forces that would be applied to your structure due to the fluids passing over it.
- Multiphase flows for situations where multiple fluids can interact with each other. These can include various liquids, liquids, gases, and bubble formation.
- High-speed flows are characterized by compressibility effects such as shock waves and expansion waves.
- Turbulence occurs at higher Reynolds numbers.
- Heat transfer can be a powerful tool for many applications, including convective cooling, evaporative cooling, and applications where a cooling process is used.
How can CFD simulation help your company?
Computational Fluid Dynamics can be used by many companies and in many forms of engineering to help you to increase your understanding of your designs, reduce development costs and turnaround times, and improve your products. Element’s CFD analysis teams can simulate the action of thermo-fluids in a system to optimize and verify the performance of your designs before developing costly prototypes and physical tests. It also enables non-destructive in-service performance improvement by assessing replacement parts and upgrades.
The Element Advantage
Our experts have experience with a broad range of flow types, including low- and high-speed flows; incompressible and compressible fluids; Newtonian and non-Newtonian behavior; laminar and turbulent flows; and multiphase systems.
We can use CFD simulation and CFD analysis to solve a variety of industrial challenges. Contact our experts for further information.
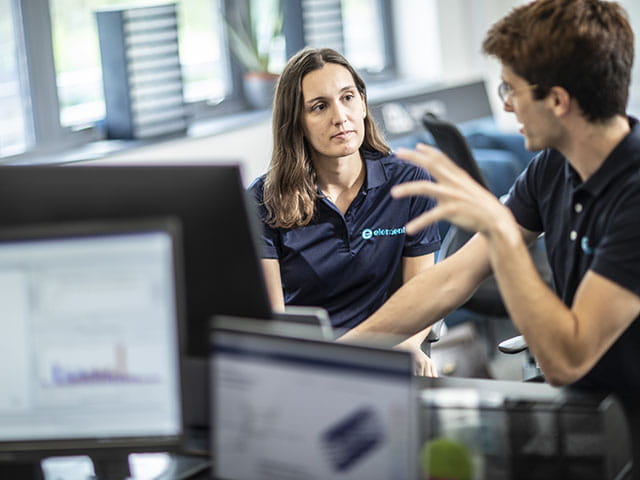
Case Studies
Element Digital Engineering utilize modeling, simulation, data science, and other digital solutions to help our customers solve complex problems.
Read examples of our work in the following sectors: aerospace, built environment, energy, marine, mining, pharma, renewables, transport, utilities.
We add value to your operations and we are always eager to support your next challenge.
READ OUR CASE STUDIES TODAYRelated Pages
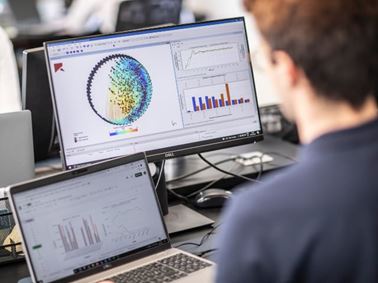
Discrete Element Method (DEM)
Our Discrete Element Method (DEM) services deliver innovative solutions that have helped companies across a wide range of industries.
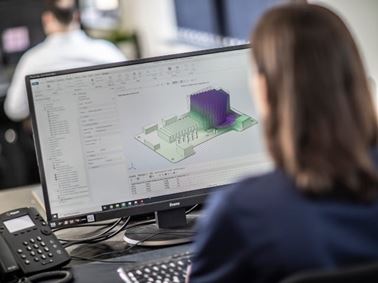
Finite Element Analysis (FEA)
Element offers advanced numerical analysis services using Finite Element Analysis (FEA) techniques utilizing industry leading software to predict the long term behavior of material components and products when in service.
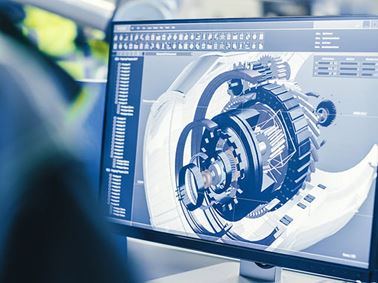
Modeling and Simulation Services
Optimize your project with our modeling and simulation services. Our expertise ensures cost-effective, compliant solutions. Enhance your project today.

Join The Digital Engineering Team
Element Digital Engineering is growing fast. We work at the forefront of Element's digital transition, delivering insight, guidance and answers to complex engineering and technology challenges. Start your Element journey today!