Enhance product reliability and ensure full compliance with ASTM E466 standards through our advanced high cycle fatigue (HCF) testing services. At Element, we specialize in accurately predicting the long-term performance of your materials under repetitive stress, providing you with the utmost confidence in the durability of your products.
What is High Cycle Fatigue Testing?
High cycle fatigue testing assesses how materials respond to cyclic forces, primarily under low applied stresses where deformation remains elastic. This testing is crucial for simulating specific scenarios and investigating real-world failures.
High Cycle Fatigue Testing Procedure
High cycle fatigue tests take place on an axial fatigue testing machine with a force-monitoring system. The sample is first machined, longitudinally polished, and ground into cylindrical or flat test specimens with a uniform or hourglass gage section. Our Engaged Experts perform alignment and verification of the machined specimen before beginning any testing.
During an HCF test, samples experience frequencies ranging between 20 Hz and 100 Hz, depending upon material types and environmental conditions. Testing continues until specimen failure or until a predetermined number of cycles is reached.
Benefits of High Cycle Fatigue Testing with Element
- Accurate Simulation of Real-World Conditions: At Element, we use state-of-the-art testing equipment to replicate the exact conditions your materials or products will face during their service life. Our HCF testing ensures that your materials are tested under varying loads, speeds, and environmental factors, providing you with precise insights into how they’ll perform in the real world.
- Early Identification of Potential Failure Points: With our expert team and advanced testing protocols, Element helps you identify your materials' weaknesses before they become costly problems. Whether it’s in design, material selection, or manufacturing processes, we ensure that your products are robust and reliable.
- Compliance with Industry Standards: We ensure your products meet industry regulations and performance standards, including ASTM E466, providing you with peace of mind and confidence in your materials.
- Enhance Product Reliability and Longevity: Our HCF testing provides essential data for optimizing your designs, ensuring products perform better and last longer.
- Versatile Testing for a Range of Materials: Alongside our High Cycle Fatigue testing Element performs a variety of other fatigue tests, including high cycle fatigue, ASTM E606 low cycle fatigue, ASTM E2368 thermo mechanical fatigue (TMF) testing and specialized programs on a range of metals and alloys, polymers, and components. We also provide indispensable High Cycle Fatigue Testing (HCF Testing) of engine airfoil and gas turbine components for service life limit analysis, simulating high vibration conditions of airfoils during operation.
Prevent Unexpected Material Failures with High Cycle Fatigue Testing
Unexpected material failures can cause costly downtime and harm your brand’s reputation. Element’s high cycle fatigue (HCF) testing simulates real-world conditions, exposing materials to low forces and elastic deformation. Conducted on advanced axial fatigue machines, our tests often exceed one million cycles and precisely monitor forces. This approach identifies potential failure points early, reinforcing material durability and ensuring reliable product performance throughout their service life.
Comply With ASTM E466 Specifications
In industries like aerospace and automotive, meeting strict safety and performance standards is crucial. Element’s high cycle fatigue (HCF) testing adheres to ASTM E466, the industry standard for force-controlled fatigue testing. We precisely machine, polish, and align specimens to ensure accurate results. By simulating various loads, speeds, and conditions, we generate data that not only meets but exceeds industry standards. This ensures your materials comply with regulatory requirements, enhancing product design and performance, and giving you confidence that your materials will surpass expectations.
Why Choose Element?
Element offers unparalleled expertise in high cycle fatigue testing. From initial specimen preparation to detailed analysis and reporting, our team of experts provides end-to-end support. Our in-depth knowledge and experience in fatigue testing ensure that you receive clear insights and recommendations to enhance your product’s performance and reliability.
Element’s dedication to meeting industry standards, such as ASTM E466, ensures that your materials are thoroughly tested and compliant with all regulatory requirements. Our thorough approach to testing enhances your product’s safety and reliability, giving you confidence in its performance.
For more information about our fatigue testing services or to request a quote, contact us today.
Multiaxial Fatigue Analysis
Multiaxial fatigue analysis replicates real-world service environments' load and stress conditions in controlled laboratory settings to develop safer materials and components.
Read moreFatigue Testing of Pipeline Girth Welds
Steel Catenary Risers are a critical element within many offshore pipeline installations. Learn more about the approach to the validation of the fatigue performance of pipeline girth welds in our whitepaper. READ MORE5 Disasters Caused by Material Fatigue
Element's fatigue testing expert discusses five disasters caused by material fatigue and what we learned from them.
READ MORERelated Services
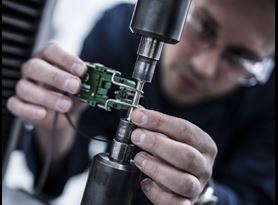
ASTM E606 Low Cycle Fatigue (LCF)
LCF testing is used for applications where materials are subject to extremely high mechanical stresses, and where plastic deformation is likely to occur.
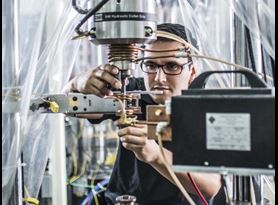
ASTM E2368 Thermo Mechanical Fatigue (TMF)
Element's ASTM E2368 thermo mechanical fatigue program provides testing services for a variety of materials qualification programs.
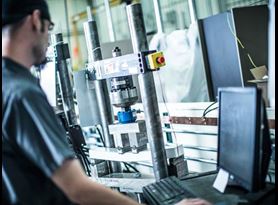
Fatigue Testing
Find out how Element's fatigue testing labs help companies meet quality requirements and create safer, stronger, more successful parts and products.
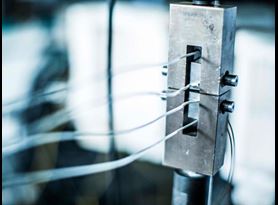
Fracture Toughness Testing
Element provides fracture toughness testing for determining material characteristics and longevity of metallic, nonmetallic, and advanced materials.