Bird Strike and Projectile Impact Testing

By Engaged Expert
David LichtmanDavid Lichtman has over 40 years of experience delivering product qualification testing to the global aerospace sector.
Aerospace qualification - bird strike testing
Relentless testing of airplane materials and components is integral to ensure planes are safe and fit for purpose. Bird strike and hail impact testing ensure when an airplane collides with a bird, hail, or debris during flight, the contact should not disable or threaten the integrity of flight capability.
Bird Strike and projectile impact testing
When an airplane collides with a bird or debris during flight, the high velocities of contact can damage or disable engines, break windscreens, and threaten the structural integrity of an aircraft. While the majority of bird strikes will not affect an aircraft to be able to continue flying, the in-flight impact can pose a serious threat and have the potential to cause significant damage, or disabling the planes ability to fly.
Aircraft certification standards for the Federal Aviation Authority (FAA) and European Union Aviation Safety Agency (EASA) require impact testing of the engine and the airframe externals. Testing the effect of impact demonstrates the resistance of the product to bird impact and can cope with damage inflicted by birds of different weights while in flight.
How to perform bird strike testing
Standardized methods for testing bird impacts include using a pneumatic cannon. A bird (usually a chicken) of a specified weight) is launched at high velocity at the Unit Under Test from a specified distance. A post-test damage assessment is then performed per the specified criteria.
Today’s bird strike testing has advanced considerably since its inception, launching birds of varying weights (1.5 to 8lbs) at velocities of up to 450mph. Proximity sensors measure the real-time velocity of each shot, and high-speed video equipment monitors each impact for further analysis.
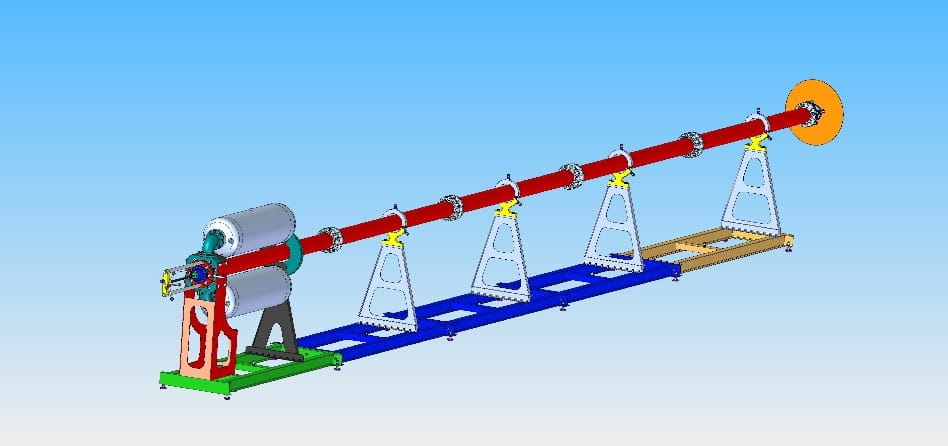
In addition to variations in speed and velocity of the projectile, there are other considerations and variables to consider when developing your test plan, including the projectile's weight, density, and rigidity, as well as the test specimens, surface shape, and angle of impact. Also, the kinetic energy absorbed by the airframe during the impact should be included during evaluation.
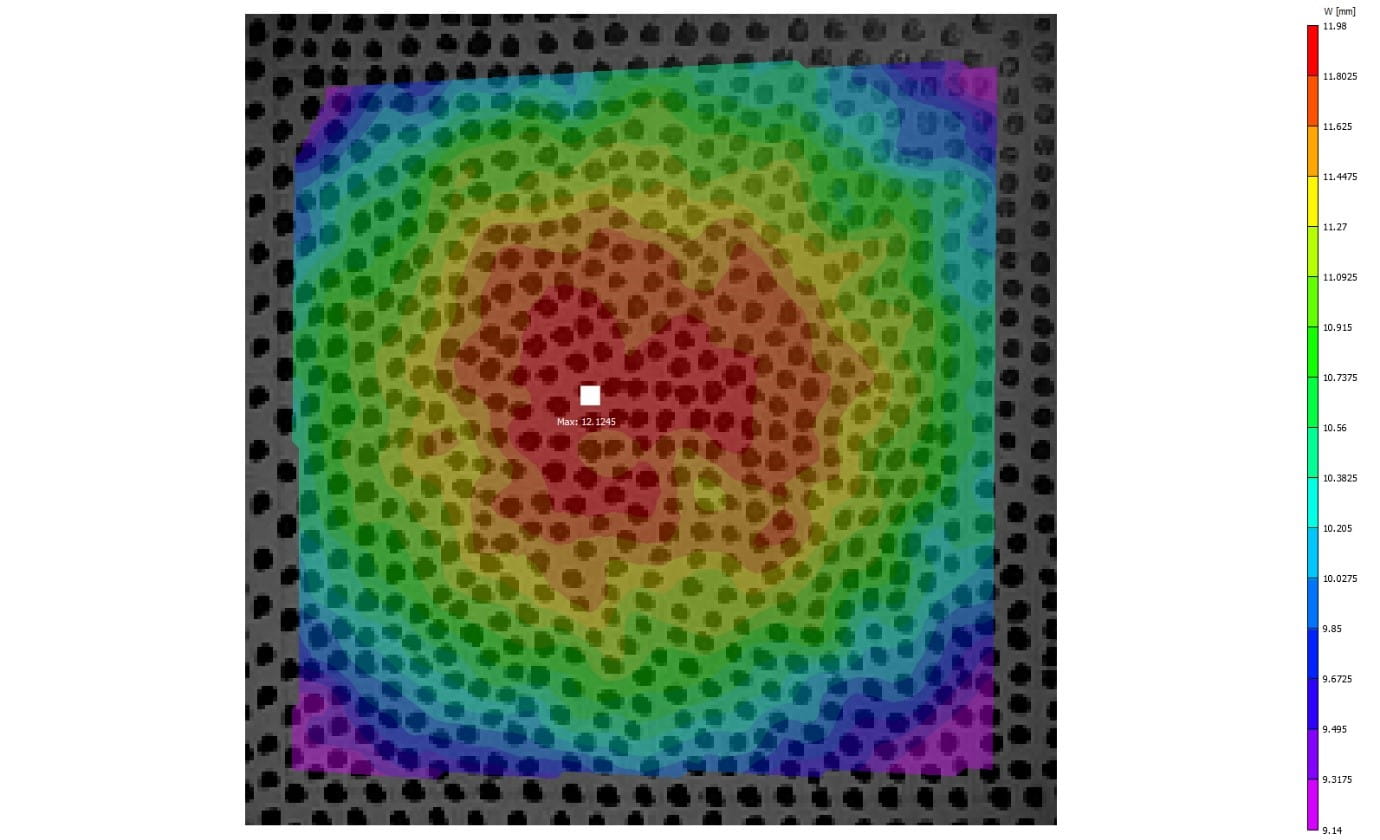
Test design for bird strike and projective testing
Element is one of only a handful of facilities in the world that is capable of offering all three types of testing (bird strike, hail impact, and projectile impact) for a wide variety of materials, components, products, and systems.
Several important factors that can influence the testing process must be taken into full consideration:
- Test Fixture Design – including the angle of the unit under test, the rigidity of the fixture, target zone of impact, instrumentation access
- Sample Preparation – Uniformity of test items, attachment points of the sample test item to test fixture
- Definition of Data Requirements - options include Strain Gaging (stress measurement), High-Speed Photography (single or multiple cameras), and DIC (Digital Image Correlation) peak displacement map.
A well-designed test program will not only make it easier to complete testing but will support a product through its complete life cycle from the development phase to post-certification. Failures during a test might result in the identification of a design weakness, which could prove fatal if not identified and rectified. Benchmarking failures in a repeatable fashion allow for new designs and improving to successful testing, and a safer product.
Combine Bird Strike Testing with Aerospace PQT
We commonly combine bird strike testing with direct & indirect lightning testing, High-Intensity Radiated Field (HIRF) testing, altitude testing, engineering simulation & finite element analysis, and explosive atmosphere testing.
With more than 3,000 technicians, engineers, and scientists dedicated to supporting our global aerospace customers, Element has the expertise and capacity to guide you through the complex nature of qualification testing of aerospace components.
Failing to meet critical deadlines such as safety of flight or late delivery can imply punitive measures and high costs. Ultimately, we deliver certainty in results, so you can create better and safer products, and minimize legal and financial risk.
Find related Resources
Related Services
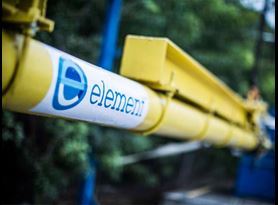
Bird Strike Testing
Find out how our aerospace experts use a bespoke cannon to simulate and launch bird strikes at aerospace components to mitigate risks for take-off and landing.
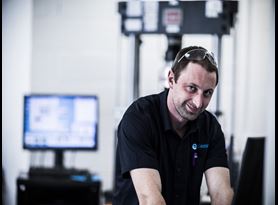
Hail Impact Testing
Element's hail impact testing programs are a critical part of your product plan to help you protect your automobiles and other vehicles from impact and.
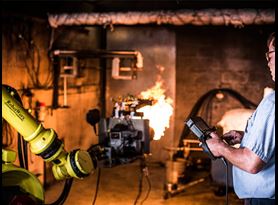
RTCA DO-160 Testing
Find out more about our extensive experience with RTCA DO 160 qualification programs, from environmental simulation to EMC testing, we are a single-source testing partner for every section of DO 160 testing.
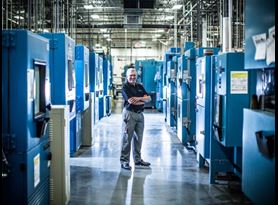
Product Qualification Testing
Find out how Element helps its Aerospace customers to develop better components, products and systems; to get them to market on time; save them time and money; and to minimize the risk associated with their product development and production activities.