Understanding Mixed Flowing Gas Testing

By Engaged Expert
Stephen TaitStephen Tait has over 19 years' experience in testing and certification of telecoms products
Mixed flowing gas (MFG) testing is an accelerated environmental corrosion aging test that provides contact with harsh chemical pollutants commonly found in the atmosphere. The test specifically evaluates the corrosion of electrical components due to exposure to atmospheric gasses and contaminants.
Why undertake mixed flowing gas testing?
Mixed flowing gas testing allows manufacturers to test for the build-up of corrosion that leads to the reduced performance of electrical components, providing an accelerated environment to determine a product’s life span as well as identify potential failure points. These results allow manufacturers to reduce premature wear and liability.
MFG testing is frequently used in conjunction with procedures which evaluate contact or connector electrical performance, such as measurement of electrical contact resistance before and after MFG exposure.
For example, this method can establish if faults such as: pore corrosion, edge effects, tendency for edge creep, plating coverage, plating integrity, and “sheltering” effect exist within the contact area.
Testing plays a key role in product development, quality control, and evaluating the risk of the premature corrosion of parts across the automotive, aerospace, consumer products and medical device industries. Taking the automotive industry as an example, products which might require MFG testing include exterior products such as tail light assemblies and engine bay products such as steering pumps and vehicle control modules.
What does MFG testing involve?
MFG testing simulates the real-world corrosion from environmental exposure conditions in a highly controlled environmental chamber. Temperature (°C), relative humidity (%RH), and concentration of gaseous pollutants and other essential variables, such as airflow and volume exchange rate, are carefully defined, monitored, and controlled in the chamber to evaluate how a product will perform under various conditions.
With distinct gaseous pollutants dominating in different field environments, Element’s team of experts can simulate virtually any environment at its Seattle-based mixed flow gas testing facilities, controlling not only the multiple-gas atmospheres at the parts per billion (ppb) level but also the temperature and humidity for the desired time limit.
Gases commonly used in the test are chlorine (Cl2), hydrogen sulfide (H2S), sulfur dioxide (SO2), and nitrogen dioxide (NO2). The concentration of each gas is controlled in the chamber to the parts per billion using mass flow meters.
Element has recently expanded its MFG testing capabilities with the introduction of an additional environmental chamber, doubling capacity and significantly increasing the volume to allow for much larger units to be tested. Its facilities comprise one of the largest chambers available within an independent testing house at 106” L x 72” W x 78” H (595k cubic inches) with a second smaller chamber of 25” L x 27” W x 52” H (35k cubic inches) also available for MFG testing.
To which standards does Element test?
The most common test standards are:
- ASTM B827 - 05(2014) Standard Practice for Conducting Mixed Flowing Gas (MFG) Environmental Tests
- ASTM B845 - 97(2018) Standard Guide for Mixed Flowing Gas (MFG) Tests for Electrical Contacts
- IEC 60068-2-60 Method 4
Most OEM specific standards usually reference IEC 60068-2-60 including Ford, FCA (Fiat Chrysler), John Deere, Volkswagen, General Motors and Daimler AG.
What preparations are required for mixed flowing gas test?
To prepare for testing, it is important to:
- Ensure no damage to units
- Ensure no corrosion present on units
- Develop a decision criteria (pass/fail)
- Determine pre/post function check procedure
Details of specification and sample size, as well as any hazardous potential, such as batteries, need to be provided before testing.
Questions?
Manufacturers frequently need advice and support for mixed flowing gas testing in the Design Validation (DV) and Production Validation (PV) process. Our experts will work with manufacturers to recommend a detailed test plan to enable them to evaluate how a product will perform in its intended storage or operating (field) environment and provide valuable expertise in overcoming potential problems.
For more information on mixed flowing gas testing, please contact an Element expert today.
Find related Resources
Get white papers, updates and event invites
Subscribe to content updates
Related Services
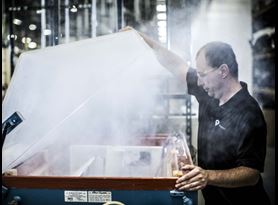
Salt Spray, Salt Fog, and Corrosion Testing
Element's corrosion testing helps you make good decisions about materials selection, treatment, and processes for virtually all industrial situations.
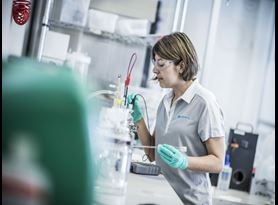
Electrochemical Corrosion Testing
Element performs electrochemical corrosion testing per ASTM F2129 to ensure that medical devices are safe, and provided the intended benefits to the patient.
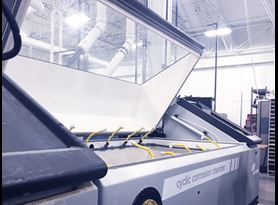
Cyclic Corrosion Testing
Find out about Element's cyclic corrosion testing services and typical variations, including sulfur dioxide salt spray, electrolyte salt spray, and seawater acetic acid testing (SWAAT).
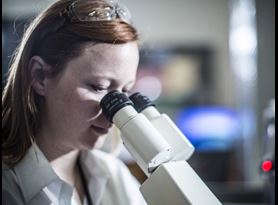
Preventing Fretting Corrosion of Orthopedic Devices
The human body is a corrosive environment that can compromise the performance of orthopedic devices. The test methods outlined in this article aid in preventing fretting corrosion in your device designs.