Thermal Shock or Thermal Cycling: What's Right for Your PCB?
There are two broad categories of thermal testing: thermal shock testing and thermal cycling testing. Both shock and cycling tests are often used to test printed circuit boards (PCBs), but when to use each type of test generally depends on whether the subject of the test is a bare PCB or a PCB assembly.
Thermal shock testing involves rapidly moving a product between two chambers, one that is extremely hot and one that is extremely cold. In the cold chamber, temperatures typically range from -40C to -55C, and temperatures in the hot chamber range from 125C to 150C. Bare PCBs are more often tested with optimized daisy chain coupons using the thermal shock method. This process allows test cycles to be completed quickly and the extended temperatures present in thermal shock testing provide an additional acceleration factor that can identify potential issues with fewer cycles. PCBs are usually tested for resistance in the high-temperature chamber, where expansion is at its peak.
Thermal cycling, on the other hand, uses a single test chamber that gradually heats up and cools down, moving the product from one extreme to the other at a rate of between 5C and 15C per minute. In this type of test, the cold temperatures can range from -25C to -40C and the hot temperatures range from 65C to 100C. Thermal cycling is more commonly used for assembled PCBs, and in many cases the assembled board is powered and tested or cycled through its operating parameters during the thermal cycling. Although thermal cycling takes longer, it is a more practical test for assembled PCBs. The rapid transitions associated with thermal shock testing can cause temperature differentials between the PCB substrate and the attached chips. This puts strain on the interconnecting solder joints, which can lead to premature joint failure, but because the extreme temperature changes present in thermal shock testing are almost impossible in a real-world scenario, it is not useful to test PCB assemblies for this type of failure. In addition, many components are not rated to perform at the more extreme temperatures typically associated with thermal shock.
Both tests cause expansion of the product and are designed to accelerate failures caused by expansion, but each has a different practical application.
It’s important to note that functional testing on assembled PCBs after thermal shock to detect failures such as cracks and IP separation can be challenging. Prior to thermal shock testing, most PCBs undergo assembly simulation to ensure consistency with the process of assembling components onto the PCBA. The rapid temperature changes during thermal shock can adversely affect solder joints due to the different rates at which components and the PCB absorb or emit heat. This can result in a coefficient of thermal expansion (CTE) mismatch between the component and the PCB, leading to solder joint failure, primarily affecting surface mount components. Additionally, certain components may be damaged by the temperatures associated with thermal shock, altering their electrical properties and potentially causing malfunction.
To address these concerns, it is essential to identify the cause of each failure observed during functional testing after thermal shock. This verification process helps determine whether the failure is PCB-related, solder joint-related, or component-related. By identifying the root cause, it becomes possible to address and rectify the specific issue, whether it involves the PCB, solder joints, or components, as any of these can lead to functional test failures.
Element is a leader in PCB testing at every stage from materials selection to regulatory approval to failure analysis. If you have questions about how PCBs or PCBAs are tested, contact our experts today.
Find related Resources
Learn more
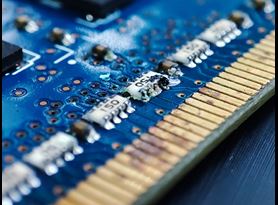
Printed Circuit Board (PCB) Failure Analysis
Understand and rectify the root causes of PCB failure with industry-leading PCB failure analysis from the testing experts at Element.

Electronic Component & PCB Assembly Testing
Element’s testing experts provide the insight you need for complex electrical component and printed circuit board (PCB) assembly testing.
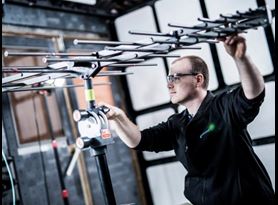
Consumer Electronics Testing & Certification
Element’s consumer electronics testing and certification services help your products meet EMC, Electrical Safety, and Radio national & global requirements.
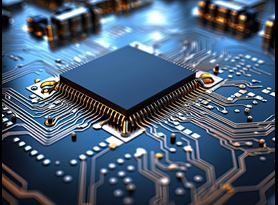
Printed Circuit Board Testing
Ensure your printed circuit boards and finished printed circuit assemblies are of the highest quality and compliant with relevant standards with comprehensive PCB testing from Element.