It is critical to understand composite damage tolerance to mitigate risk and ensure the material is fit for purpose. Despite their high strength and durability properties, composite materials are still susceptible to in-service damage.
Composite damage tolerance is the capability of a damaged structure or laminate to maintain its original stiffness and strength. Composite structures may be damaged during production or in-service, and those damages aren’t always visible during later inspections.
Element offers a variety of test methods that provide you with more insight into your composite materials’ damage tolerance and resistance and how that damage may grow during service. Two common methods are drop weight impact testing and fracture toughness testing.
Drop weight impact testing of composites
Drop weight impact testing assesses the damage resistance of the material against different impact energies. The method involves dropping a known mass from a known height, perpendicular to the face of a composite specimen.
Impact testing provides information about the resistance of a composite to impact damage and can be used in conjunction with Compression After Impact (CAI) testing to determine damage tolerance. CAI results show how an impact affects the subsequent compression strength of the material.
After impact, non-destructive inspection methods help measure the depth and size of the damaged area. Achieving Barely Visible Impact Damage (BVID) provides insight into the level force a composite can tolerate before it is no longer fit for purpose.
Fracture toughness testing of composites
Composite materials have lower through-thickness tensile and shear strength than traditionally manufactured materials, meaning out-of-plane loading may cause delamination. Regardless of interlaminar strength, fracture toughness is a property that determines how likely it is that delamination will propagate further.
Fracture toughness testing of composites involves using a specimen with pre-crack (e.g. a release film embedded within the laminate), that simulates an in-service crack. During testing, a load is introduced to force the crack faces apart in either:
- Mode I (crack opening)
- Mode II (crack shear)
- Mode III (crack scissoring)
Some test standards call for using mixed modes such as a combination of Mode I and Mode II crack growth.
The Element advantage
Element’s material testing experts have a breadth of experience in evaluating composite damage tolerance and durability. We work diligently to ensure your composites meet the requirements of relevant industry and custom test standards.
For more information on how we can help you better understand the damage tolerance of your composites or to request a quote, please contact us today.
Related Services

Shear Testing of Composites
Our composite testing experts provide shear testing methods including interlaminar, in-plane, and v-notch to measure the shear properties of your material.

Examining Fiber-Reinforced Composite Materials
Microscopic and macroscopic examination of fiber-reinforced composite materials helps ensure the quality of the material early in the manufacturing process.
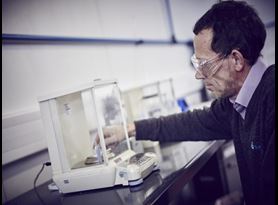
Polymers Testing
Element performs a range of mechanical, electrical, flammability tests and utilizes thermal analysis tests to characterize the composition of polymers and composite materials.
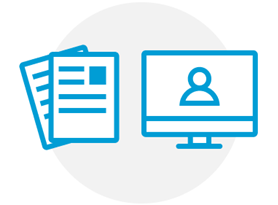
Sign Up for Free Resources
Visit Element's email subscription center to receive the latest industry news, technical whitepapers, case studies, webinars, and upcoming events.