Element’s water immersion testing services evaluate a coating’s resistance to in-service immersion conditions. This helps determine the coatings suitability for corrosion protection during its service life.
Immersion testing
Immersion tests form the basis of many different standards, as well as being standalone tests in their own right.
The basic test involves a coated test sample being fully or partially immersed in water, at ambient conditions or at elevated temperatures and pressures. The coated samples are then assessed for any signs of degradation, including blistering, cracking, and adhesion loss.
Water Immersion testing methods
Meet industry standards - partner with Element to test to a wide range of immersion testing methods, including:
Ambient water immersion methods:
- ISO 2812-2 – determination of resistance to liquids – Part 2: water immersion method
Standards which incorporate this test include:
- Norsok M-501
- ISO 12944-6
- ISO 12944-9 - ASTM D870 – water resistance of coatings using water immersion
- NACE TM0104, TM0204, TM0304 and TM0404 – a suite of standards for offshore installations
Elevated temperature water immersion methods:
- ISO 21809-1 – buried or submerged pipelines – hot water immersion
- ISO 21809-2 – buried or submerged pipelines – hot water adhesion
- ISO 21809-3 – buried or submerged pipelines – hot water immersion
- CSA Z245.20&21 – pipe coatings – hot water adhesion
- NACE TM0174 – evaluation of coatings in immersion service
- ASTM D6943 – immersion testing of industrial protective coatings and linings
Elevated temperature and pressure water immersion methods:
- NACE TM0174 (Modified) – modified to allow elevated pressure as well as temperature and also gas mixes
- Autoclave – various size vessels cover a wide range of temperatures, pressures and gas mixes
Water absorption testing:
- ISO 62 – Determination of water absorption
- NACE TM0104 and TM0204 – Dimensional stability
Custom water immersion testing:
In addition to the above test standards, Element can perform bespoke testing to meet individual project requirements and can carry out a wide range of immersion testing.
Why choose Element?
With fully ISO 17025 compliant testing laboratories worldwide - in Europe, North America and Asia - Element offers a wide range of testing for coatings evaluation including water immersion testing. From Aerospace and Oil & Gas to Transportation and Infrastructure, we deliver high quality and dependable results to our clients in many industries worldwide.
For further information on water immersion testing, or to request a quote, please contact our experts today.
Failure Analysis of Pipeline Coatings
This free white paper includes an extensive case study of the failure analysis of a 12-inch diameter Fusion Bonded Epoxy (FBE) coated steel pipe that showed blistering of the coating and corrosion on the surface.
Read MoreStandard Update: Norsok M 501 edition 7
One of the most important standards for coatings testing in the oil and gas industry has undergone a major revision. This article explains the consequences for manufacturers and testing requirements.
Read MorePaints and Coatings Failures: A Guidebook on Causes and Remedies
Failure analysis is a valuable tool when investigating the root causes of asset failure, and developing a corrective action plan to ensure your paints and coatings adhere and remain intact.
READ MOREReady to request a quote?
Our deliverable is certainty - high quality data, test reports and certificates that you can absolutely rely on when making decisions about your materials and compliance. Engage with an expert today.
Related Services
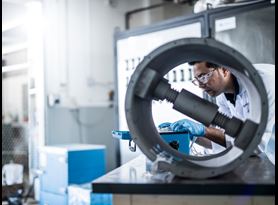
Sour Service Corrosion Testing
Element is one of a few ISO certified sour service labs in the world, providing sour service corrosion services for a variety of test types including NACE MR0175/ISO 15156.
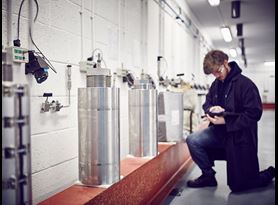
HPHT Testing
Find out how Element helps its customers to choose the right polymeric materials for use in seals, gaskets, flowlines and pipeliners that are capable of lasting over 20 years in harsh environmental conditions.
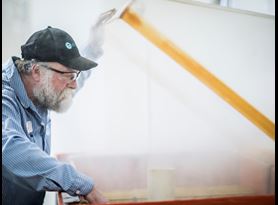
ISO 12944
Element offers testing to international standards ISO 12944-6 and 12944-9 (formally ISO 20340) to aid in the selection of suitable paint systems for corrosion protection.
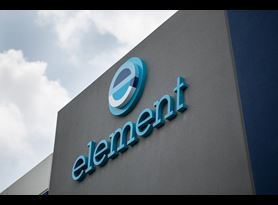
Local laboratories, global platform
Doing business with one of our laboratories enables our clients' access to our global platform of expertise, capacity and capabilities.