Carbon capture and storage (CCS) is a relatively new technology to store pressurized carbon dioxide underground. One of the challenges is to keep pipelines and injection tubes safe and prevent corrosion. Element supports corrosion testing of metallic components and examines polymeric materials to reduce transport costs and avoid failure.
With the increased concern of carbon dioxide (CO2) on the environment, reducing carbon emissions into the atmosphere is now a major focus for most industrialized countries. Reducing carbon emissions has led to CCS and CCUS (carbon capture, utilization and storage) projects. The projects have predominately been in the USA and Canada for Enhanced Oil Recovery (EOR), but there is a growing demand in Europe, Asia and the Middle East.
Numerous global projects in the planning stage are operational as pilot, research, and development plants in most countries where CO2 is produced. Most CCS/CCUS projects aim to capture CO2 and store it below the surface, mainly in offshore locations.
Corrosion of CCS transportation pipelines
For metals used in the CCS/CCUS infrastructure, the corrosion or cracking of the carbon steel transportation pipelines and carbon steel or corrosion resistant alloy (CRA) injection tubing is the primary concern of potentially corrosive environment.
The risk of corrosion/cracking needs to be evaluated on a case-by-case basis since it’s severity will depend on the material and the specific levels of H2O, O2 and acidic gas impurities of CO, H2S, SOx, and NOx in the dense phase CO2.
In order to mitigate carbon steel corrosion in CCS transport pipelines, the use of corrosion inhibitors can be considered. However, their effectiveness would be dependent on the specific conditions, so would require qualification testing.
Corrosion Testing for CCS infrastructure may be required to evaluate the resistance of the materials to:
- CO induced Stress Corrosion Cracking (SCC) of carbon steels (Transportation pipelines)
- H2S induced Sulfide Stress cracking (SSC) of carbon steels (Transportation pipelines)
- H2S induced Stress Corrosion Cracking of CRA’s (Injection tubing/casing)
- General corrosion of carbon steels (Transportation pipelines)
- Pitting corrosion of corrosion-resistant alloys-CRA’s (Injection tubing/casing)
Testing polymeric materials
The main concerns in the use of polymeric materials for seals, linings, etc. in the CCUS infrastructure are:
- the physical effects of CO2 on those materials, for example swelling and weakening
- rapid gas decompression (RGD) damage such as blistering, cracking, splitting
- chemical resistance to gas impurities - the influence of contaminants on the long term integrity of the materials
- the high pressure and low temperature operating conditions for CCUS can be a limiting factor to the use of some polymers
- loss of product or environmental issues caused by permeation of CO2 through polymeric seals and liners
The Element advantage
Our centers of excellence for the Energy sector are located in the US and Europe. The locations are fully equipped to perform corrosion testing and electrochemical testing on metallic components and polymeric materials used for CCS/CCUS infrastructure.
For more information about our corrosion testing services for CCS/CCUS projects, or request a quote, contact us today.
Whitepaper: Rapid Gas Decompression (RGD) Tests Involving Hydrogen Sulfide
This white paper demonstrates that H2S is a more hostile gas than CO2 towards housed elastomeric seals subjected to repeated pressure cycling in RGD tests.
Read MoreUnderstanding Mixed Flowing Gas Testing
Mixed flowing gas (MFG) testing is an accelerated aging test that specifically evaluates the corrosion of electrical components due to exposure to atmospheric gasses and contaminants.
Read MoreFracture Mechanics in Sour Service: Some Characterization Tests on SENT and SENB Specimen
This article provides better understanding of how the SENT test technique influences fracture toughness of pipelines in sour service environments.
Read MoreWebinar: Corrosion of Stainless Steel
This webinar shows examples of corrosion damage and guides you through how to avoid corrosion in your stainless steel products to prevent product failure and costly repairs.
Watch NowEmissions Monitoring on Carbon Capture Site
Read how our emissions team are using industry-leading instrumentation such as SIFT-MS to accurately measure the chemical composition of post-combustion flue gases at carbon capture plants.
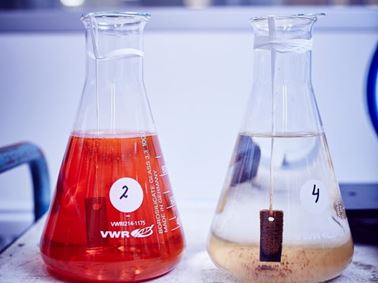
Corrosion Testing ServicesÂ
Find out about Elements extensive corrosion testing expertise in the Energy industry across a global network of laboratories.
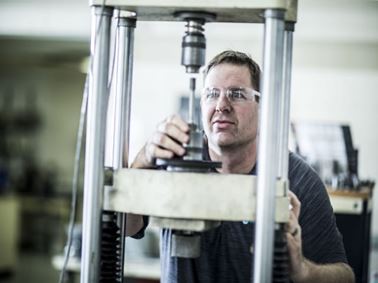
Structural Testing & Mechanical Engineering
Element offers a range of advanced and application oriented engineering services to help solve a wide variety of mechanical engineering and structural engineering analysis problems.
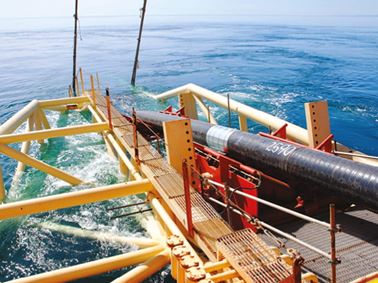
Coatings Testing
Find out about Elements range of coatings testing services designed to help to make certain that materials, products and pipelines we test for our customers are protected from corrosion, ultraviolet light, water penetration, heat, abrasion and chemicals.
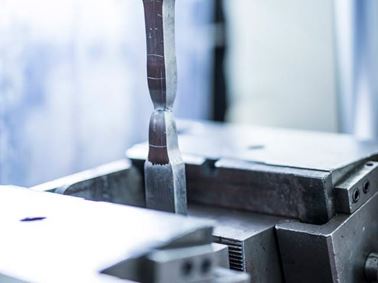
Materials Testing
Find out more about Element's comprehensive ranges of materials testing services available in the TIC sector, covering materials selection, application and performance testing as well as failure analysis testing services.
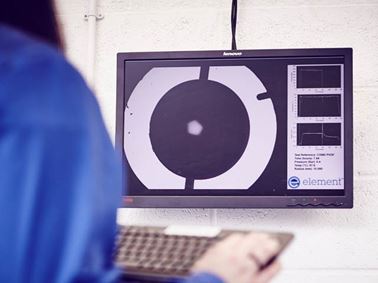
Supercritical CO2 (scCO2)
Element supports the energy industry in managing the challenges of polymeric materials like in service in supercritical CO2 (scCO2) environments.
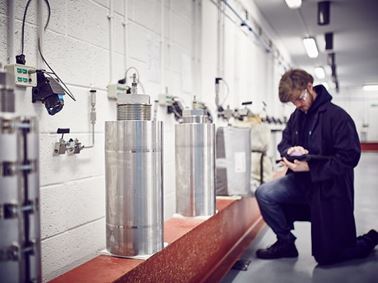
High Pressure High Temperature (HPHT) Exposure Testing Services
We offer extensive services for the qualification and compatibility of polymer materials exposed to production fluids at high pressure and high temperature (HPHT).
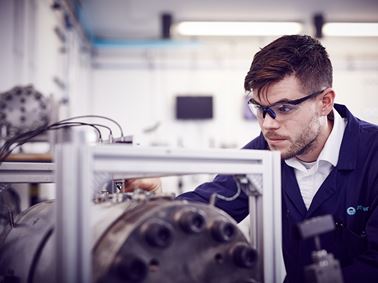
Permeation & Diffusion Testing
With a unique range of permeating capabilities for polymers, thermoplastics, elastomers and composites, we can simulate the high pressure and extreme temperatures found in deep wells, or the conditions in an automotive applications, utilities industry or chemical processing equipment.
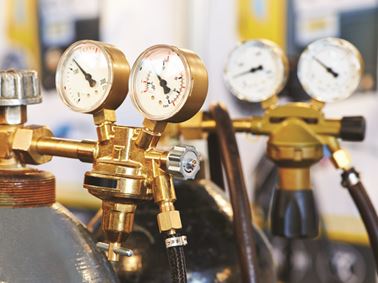
Rapid Gas Decompression Testing (RGD)
Element offers rapid gas decompression testing to help manufacturers and users of elastomers better understand the behavior of this material in true sour RGD conditions.