Magnetic particle inspection (MPI) also known as magnetic particle testing (MPT) is a non destructive test (NDT) method used to check for surface and near-surface discontinuities in ferrous materials. Our magnetic particle testing is performed on-site or in one of our state-of-the-art laboratories.
Because this method relies on a magnetic field to produce results, it works best on ferrous materials, like nickel, iron, cobalt, and some alloys. Components like billets, bars, castings, forgings, fasteners, weldments and extrusions are also commonly tested using magnetic particle inspection.
Magnetic particle inspection methods
Trust the NDT Experts at Element
Magnetic particle inspection can be performed using a wet or dry method, depending on the application. In both methods, the product is electrically charged to create a magnetic field. Then, ferrous iron particles are applied to the part in a dry or wet suspension.
If there is a crack or other defect present, the particles will be attracted to the flaw and build up around the leakage to for an “indication.” The indication is then evaluated to determine the characteristics and cause of the defect. Results allow our Engaged Experts to understand the type and severity of any discontinuities on the part’s surface or sub-surface.
Why choose Element for MPI testing?
By examining the nature, location and extent of an indication, our highly trained and experienced inspectors can determine the origin and cause of both surface and near-surface discontinuities.
Element operates full-service non-destructive testing (NDT) and magnetic particle inspection laboratories that utilize advanced equipment capable of performing quality inspections for virtually any form of ferrous material, component or assembly.
For more information about our magnetic particle testing or to request a quote, contact us today.
Our magnetic particle testing equipment
Ready to request a quote?
Our deliverable is certainty - high quality data, test reports and certificates that you can absolutely rely on when making decisions about your materials and compliance. Engage with an expert today.
More from Element
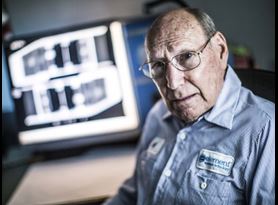
Radiographic Inspection Services
Element’s radiographic inspection laboratories provide testing for a wide array of sectors. Our global experts advise on the most suitable testing methods to ensure your materials and products are fit for purpose.
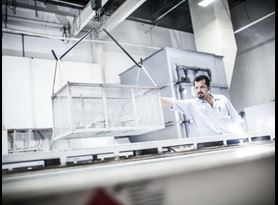
Liquid Penetrant Inspection (LPI)
Liquid penetrant inspection (LPI), or dye penetrant inspection, is a reliable and cost-effective method for detecting surface flaws of welds, castings, and other components that cannot be destroyed. Our experts can conduct comprehensive on-site penetrant inspection.
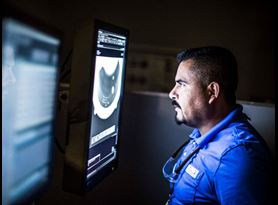
Non-Destructive Testing (NDT)
Element's NDT services comply with a wide variety of industry standards, government contracts, military specifications and unique customer requirements.
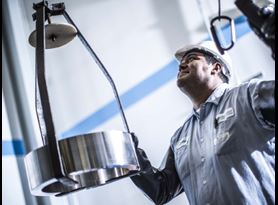
Ultrasonic Testing (UT)
Our inspectors use ultrasonic waveforms to pass through a material to detect flaws and provide a complete volumetric inspection. Contact testing, Phased Array and the Immersion technique are available for complex geometric parts that otherwise may not be subject to complete volumetric inspection.