Liquid penetrant inspection (LPI), or dye penetrant inspection, is a reliable, efficient, and cost-effective method for detecting surface flaws of welds, castings, and other components that cannot be destroyed. LPI or dye penetrant is a portable surface inspection method, allowing our Engaged Experts to conduct comprehensive onsite evaluation.
What is liquid penetrant inspection utilized for?
Liquid penetrant inspection is a valuable tool for evaluating non-ferromagnetic and non-metallic materials. In addition to utilizing dye in checking for defects and cracks, it can also be used to determine other surface characteristics, such as porosity.
The dye penetrant inspection process
Parts must go through a pre-cleaning process (etch, alkaline or solvent-cleaning) before the liquid penetrant is applied. After allowing proper dwell time, excess penetrant is removed from the surface (but not from any possible defects), and the part is dried. Then a developing powder is applied; this developer pulls up the dye that has seeped into cracks or pores, resulting in visible marks or indications that identify surface flaws. Based on the results, an inspector then provides a report with the type, number and size of defects on a component.
Element's LPI capabilities
- A 55’ x 15’ wet room equipped with a 2.5-ton hoist for processing large specimens
- All methods of dye penetrant inspection, including lipophilic and hydrophilic emulsified systems, as well as water washable and solvent removable to meet any sensitivity requirements
- Certification by major prime contractors for the inspection of fracture critical hardware
- In-house chemical etching services, which allows for "one-stop lab" processing
- Global network of conveniently located labs, including Element Altbach, located in Germany offering high-volume Liquid Penetrant Inspection with a capacity of up to 12,000 parts per day
Why choose Element for liquid penetrant inspection (LPI)?
Our non-destructive testing (NDT) experts are well-trained in liquid penetrant inspection and hold Level II and III certifications from ASNT, among other qualifications. Element provides Type II non-fluorescent NDT services to all of the various commercial and nuclear codes, as well as Type I fluorescent inspection to aerospace, government, nuclear, and after-market applications.
For more information about our liquid penetrant inspection services or to request a quote, contact us today.
“Excellent on-time delivery.”
Steve Lerma
74 Weld
Ready to request a quote?
Our deliverable is certainty - high quality data, test reports and certificates that you can absolutely rely on when making decisions about your materials and compliance. Engage with an expert today.
More from Element
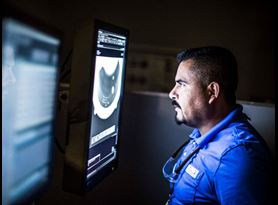
Non-Destructive Testing (NDT)
Element's NDT services comply with a wide variety of industry standards, government contracts, military specifications and unique customer requirements.
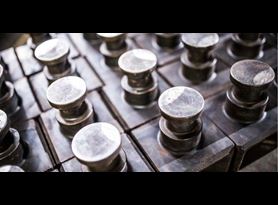
Magnetic Particle Inspection (MPI)
Magnetic particle inspection (MPI) is a non destructive test (NDT) method used to check for surface and near-surface discontinuities in ferrous materials. Our testing is performed on-site or in one of our state-of-the-art laboratories.
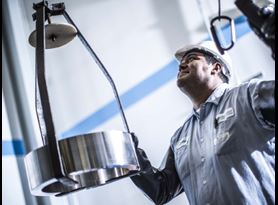
Ultrasonic Testing (UT)
Our inspectors use ultrasonic waveforms to pass through a material to detect flaws and provide a complete volumetric inspection. Contact testing, Phased Array and the Immersion technique are available for complex geometric parts that otherwise may not be subject to complete volumetric inspection.
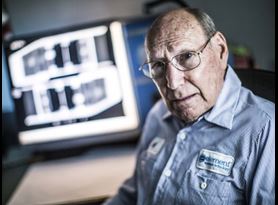
Radiographic Inspection Services
Element’s radiographic inspection laboratories provide testing for a wide array of sectors. Our global experts advise on the most suitable testing methods to ensure your materials and products are fit for purpose.